In our relentless pursuit of unlocking the fascinating universe of 3D printing, we stand at the threshold of a multitude of groundbreaking technologies, each endowed with unique capabilities that shape the landscape of additive manufacturing. From the pioneering Fused Filament Fabrication (FFF) to the awe-inspiring Digital Light Synthesis, these technologies have ushered in a new era of design, prototyping, and production.
Fused Filament Fabrication (FFF) / Fused Deposition Modeling (FDM)
In the realm of 3D printing, Fused Filament Fabrication (FFF) reigns as a hallmark of accessibility and versatility, capturing the imagination of novices and experts alike. Its fundamental principle revolves around the extrusion of thermoplastic filaments through a heated nozzle, shaping layer upon layer of material into intricate forms.
- Mechanism: FFF operates on the bedrock of additive manufacturing, constructing objects by adding material layer by layer. The thermoplastic filaments are fed into a heated nozzle, where they melt and are precisely deposited onto the build platform.
- Materials: FFF embraces a broad palette of thermoplastic materials, encompassing ABS, PLA, PETG, and beyond. This diversity empowers creators to tailor their prints to the specific needs of their projects.
- Applications: The inherent simplicity and cost-effectiveness of FFF have positioned it as a favored choice for rapid prototyping, functional concept models, and educational contexts. The vibrant maker community has found solace in the user-friendly nature of FFF, fostering a culture of exploration and creation.
Stereolithography (SLA)
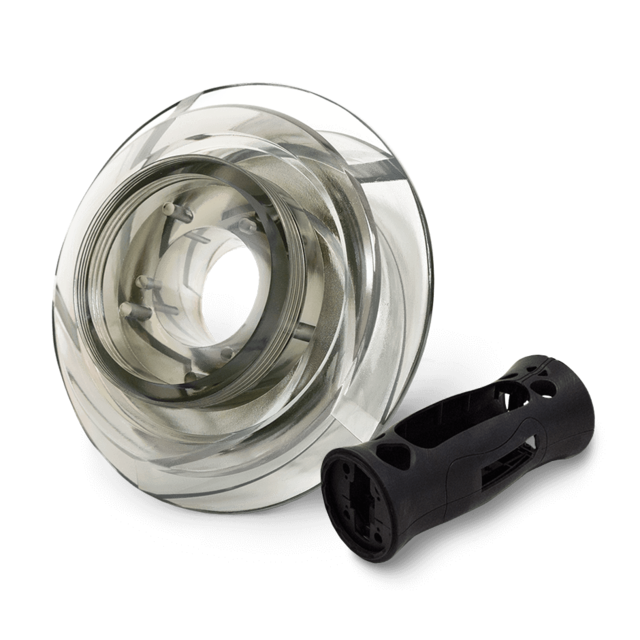
Venturing back to the genesis of 3D printing, we encounter the iconic Stereolithography (SLA), a trailblazing technology that laid the foundation for the additive manufacturing revolution. Harnessing the potent force of light, SLA transforms liquid resin into solid structures, unfurling layers of innovation with each pass.
- Mechanism: In SLA, a precise ultraviolet laser scans the surface of a liquid photopolymer resin, inducing polymerization and solidification. This process repeats for every layer, culminating in the fabrication of a complete three-dimensional object.
- Materials: SLA predominantly employs photopolymer resins that undergo rapid polymerization when exposed to ultraviolet light. These resins span a gamut of formulations, offering diverse attributes such as toughness, flexibility, and transparency.
- Applications: Renowned for its precision and ability to craft intricate details, SLA finds its calling in domains such as jewelry design, dentistry (for creating accurate dental models and molds), and microfluidics.
Selective Laser Sintering (SLS)
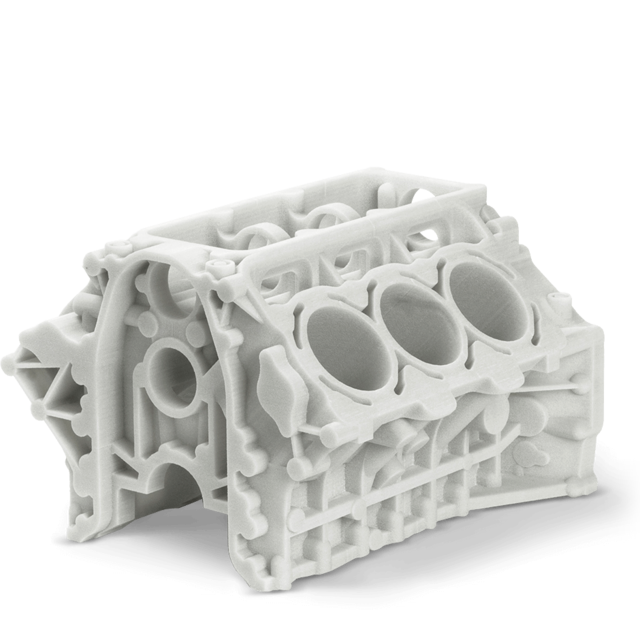
Among the stalwarts of industrial additive manufacturing stands the formidable Selective Laser Sintering (SLS), a technology that wields a high-powered laser to selectively fuse powdered materials into fully formed structures, layer by meticulous layer.
- Mechanism: SLS orchestrates a choreography of laser scanning and material fusion. The unforgiving laser beam scans the surface of a bed of powdered material, causing localized fusion. Unfused material acts as a temporary support structure for overhanging features and intricate geometries.
- Materials: SLS embraces a diverse spectrum of materials, spanning plastics, metals, ceramics, and composites. This versatility renders it an indomitable force in producing aerospace components, bespoke medical implants, and functional prototypes.
- Applications: The robustness and dimensional accuracy of SLS render it indispensable in industries that demand sturdy and high-performance parts, exemplified by its integration into the automotive and aerospace sectors.
MultiJet Printing
MultiJet Printing emerges as a versatile contender, leveraging its inkjet-inspired mechanism to deliver exquisite precision and finesse, akin to an artist's brushstroke.
- Mechanism: MultiJet Printing entails the layer-by-layer deposition of liquid photopolymer material through an inkjet-style printhead. Ultraviolet light swiftly cures each layer, bestowing it with permanence and structure.
- Materials: The technology harnesses an array of photopolymer resins, each calibrated to cater to specific applications, such as dental models, jewelry fabrication, and intricate product design.
- Applications: The ability to produce objects with a seamless, smooth surface finish and fine details positions MultiJet Printing as an indispensable tool in fields that value meticulous craftsmanship and precise outcomes.
Digital Light Processing (DLP)
In the family of light-based 3D printing, Digital Light Processing (DLP) emerges as a close relative to Stereolithography, wielding its own unique advantages while capitalizing on the speed and efficiency offered by digital light projectors.
- Mechanism: DLP leverages a digital light projector to expose an entire layer of liquid photopolymer resin to light simultaneously. The layer solidifies promptly, propelling the printing process with enhanced velocity.
- Materials: The photopolymer resins utilized in DLP are akin to those in SLA, ensuring that high-detail prints and excellent surface finishes are consistently achievable.
- Applications: DLP finds its niche in applications where speed and precision are paramount, making it a potent tool for a diverse range of prototyping requirements.
Other 3D Printing Technologies
The panorama of 3D printing technologies unfurls further, unveiling a pantheon of capabilities that continue to push the boundaries of creativity and innovation:
- Material Jetting: Riffing on inkjet technology, Material Jetting employs precision nozzles to deposit liquid photopolymer materials layer by layer.
- Binder Jetting: This technique binds layers of powdered material using a liquid binder, enabling the creation of full-color prints and molds.
- Powder Bed Fusion: Through the guidance of a laser or electron beam, Powder Bed Fusion selectively fuses powdered material, engendering robust and resilient parts.
- Electron Beam Melting: Siblings to Powder Bed Fusion, Electron Beam Melting employs an electron beam within a vacuum environment to melt metal powders, resulting in intricate and complex metal structures.
- Laminated Object Manufacturing: This method binds layers of adhesive-coated paper, plastic, or metal sheets together, bringing life to multi-layered objects.
- Continuous Liquid Interface Production: Crafting objects using a liquid interface and a dynamic moving platform, Continuous Liquid Interface Production seamlessly bridges layers for a smooth finish.
- Digital Beam Melting: A focused electron or laser beam melts metal powder, unveiling the potential for detailed and durable metal components.
- Digital Light Synthesis: A high-speed, continuous 3D printing process that employs light and oxygen to swiftly solidify liquid resins, epitomizing the fusion of speed and precision.
The sheer expanse of 3D printing technologies stands as a testament to human ingenuity, fostering a limitless spectrum of possibilities across industries and domains.
On Demand Manufacturing at 3D Technology Ltd.
No other Irish service bureau offers the complete suite of manufacturing services the way we do. From 3D printed prototypes to final production, we provide additive manufacturing services such as Stereolithography (SLA), Selective Laser Sintering (SLS), MultiJet Printing (MJP), Fused Deposition Modeling (FDM) and Direct Metal Printing (DMP) as well as subtractive technologies, such as CNC machining, Injection Moulding, Sheet Metal Parts, Metal Die Casting and Investment Casting.
Learn more: https://www.3dtechnology.ie/on-demand-manufacturing