THE CUSTOMER
**Honest work, uncompromising quality, and a solution-oriented approach.**
Since 1978, Toivalan Metalli has upheld its mission to tackle any metal job, big or small, with the tools and flexibility to meet clients' needs for custom components. Their services include laser cutting, pipe bending, welding, and more, serving a diverse customer base in construction, elevator manufacturing, machinery, weather protection, and furniture industries. This well-established Finnish machine shop has continually evolved, prioritizing customer orientation by genuinely listening to customers and offering versatile, reliable, and high-quality services.
THE CHALLENGE
To address their need for independence and control over steel tooling for process and design validation, Toivalan Metalli partnered with Vossi Group. Staying updated with production equipment and technological advancements is crucial in today's service industry, and Toivalan Metalli has consistently invested in advanced manufacturing technologies. These investments include fiber lasers, disk grinding, edge turning machinery, CNC pipe bending, and pipe end forming machinery, propelling their business forward.
Despite these advancements, a significant challenge remained: handling low-volume, custom projects. Many jobs required specific bending tools, driving part costs up to €4,000 due to the need for custom tube bending dies from major suppliers. This was not only costly but also slowed projects due to dependencies and supply chain issues.
“Before introducing additive manufacturing (AM), when customers asked us to make a special radius, there was a lot of guesswork involved, and occasionally we had to reject the project. Now, we’ve completely shifted our way of looking at requests. We can easily prototype and see if it works with the pipe. We even use it for end-use parts.”
– Toni Pasanen, Manager, Welding Shop, Toivalan Metalli
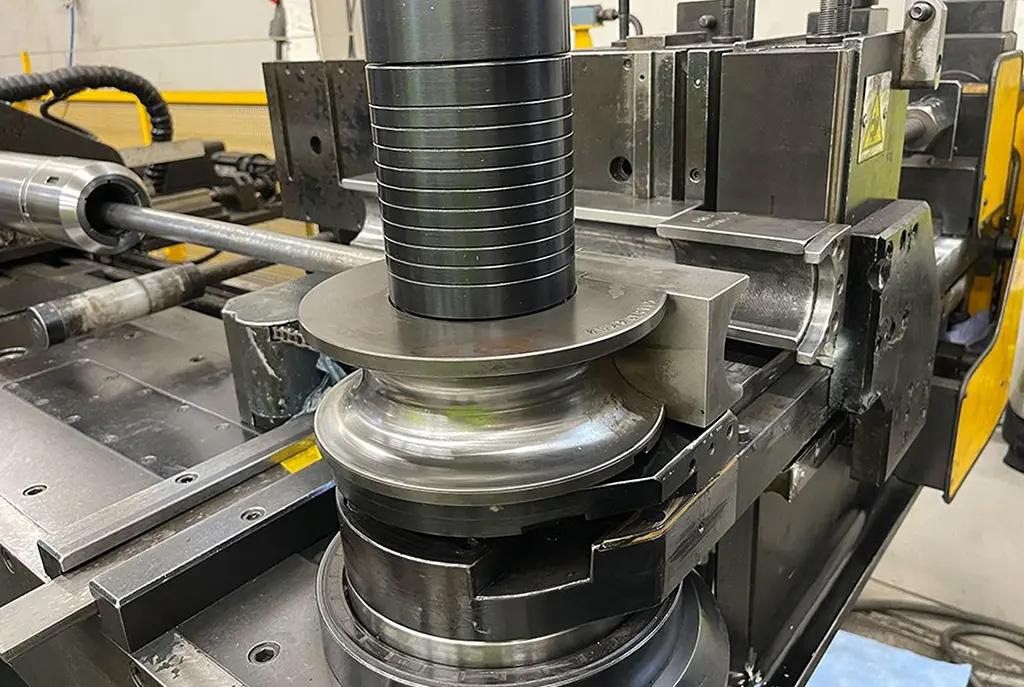
THE SOLUTION
Instead of paying premiums for low-use steel prototypes, Toivalan Metalli now prints tools on their Markforged X7 printer—strong enough for several bending runs before needing to purchase the final die. Originally intended to endure ten bending runs, these custom tools now achieve nearly 500 runs by adapting designs and integrating off-the-shelf hardware, handling 25-30mm diameter, 1.5mm wall thickness steel tubes with a 70mm bend radius.
Using the X7, Toivalan Metalli primarily produces tube-bending tools. Previously, these tools cost around €4,000 with a six-week lead time when purchased from OEMs. Now, they print functional prototype bending tools for low-volume production as needed, reducing the price per part to €300-€400 with a maximum lead time of one week.
“The threshold is minimal. The X7 is simple to use, and basic training can be completed in just one day.”
– Toni Pasanen, Manager, Welding Shop, Toivalan Metalli
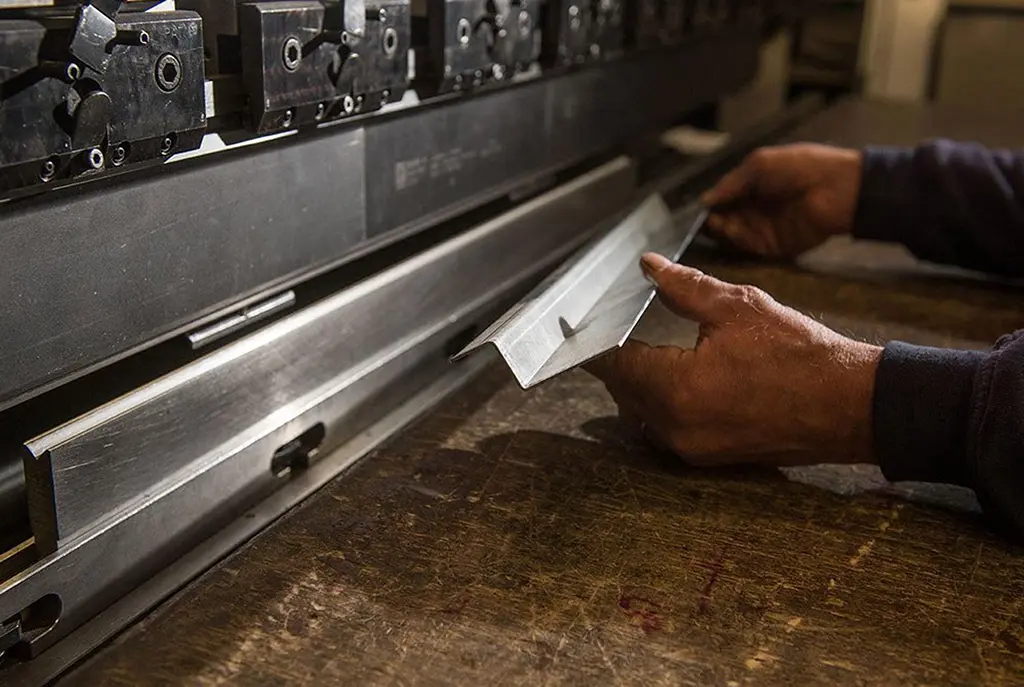
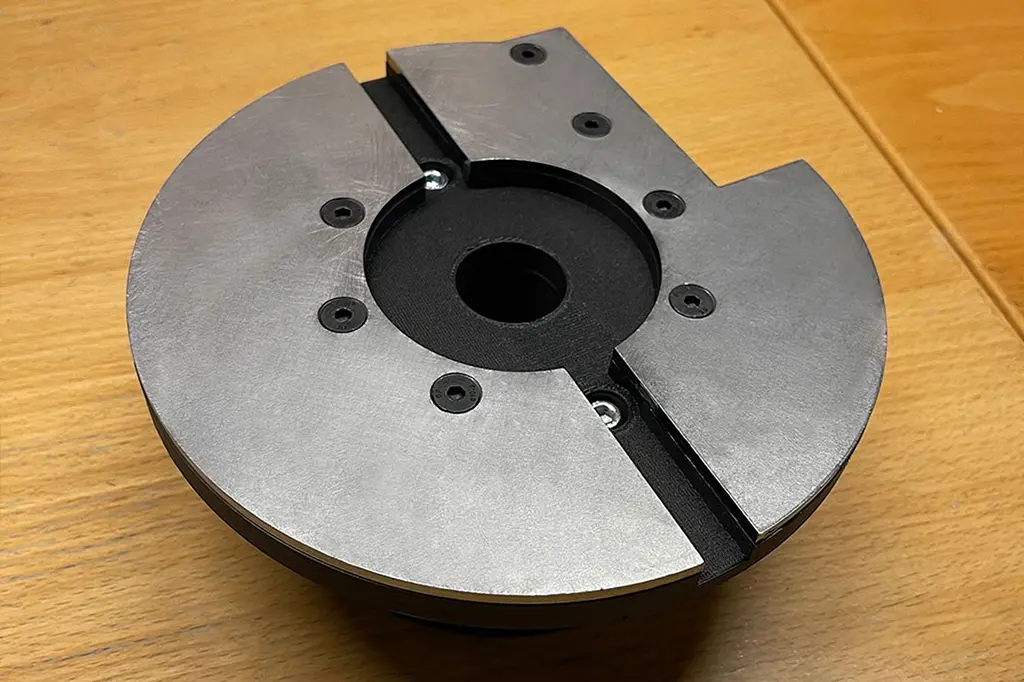
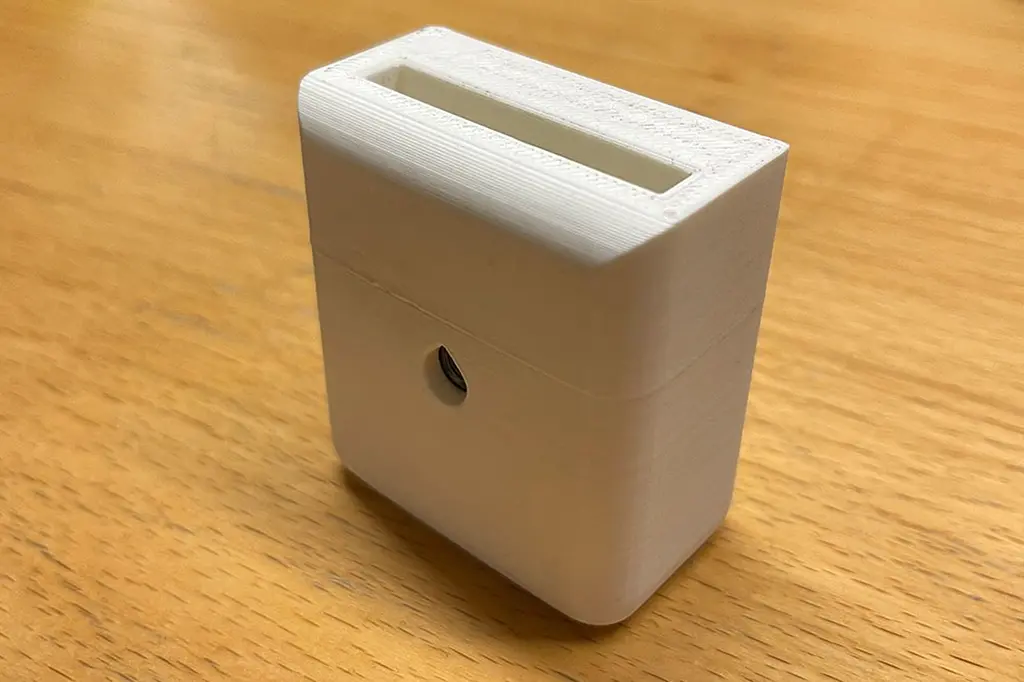
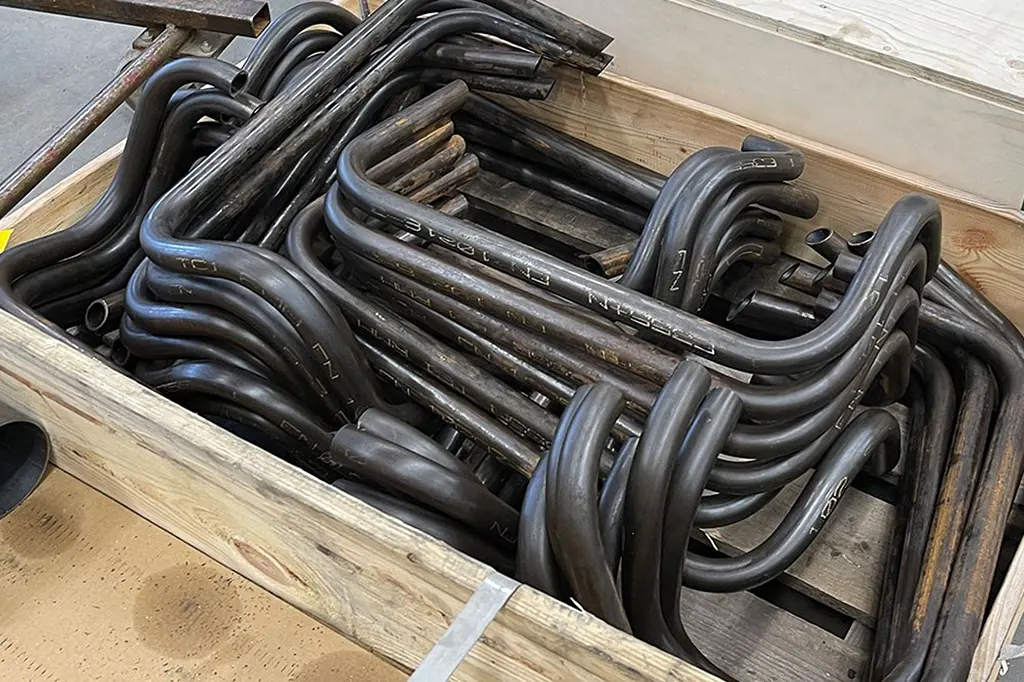
CONCLUSION
Main Benefits for Toivalan Metalli:
- **90% Cost Savings:** Significant reduction in tooling costs.
- **Reduced Lead Times:** Digital inventory through Eiger slashes production timelines.
- **Faster Reaction Time:** Quick turnaround for custom requests.
- **New Revenue Streams:** Ability to handle low-production runs efficiently.
THE FUTURE
Toivalan Metalli continues to innovate with the Digital Forge, enhancing the strength of printed tools by embedding bolts and reinforcing them with continuous carbon fiber. This capability has attracted more low-volume business, bringing in tens of thousands of euros in additional revenue over three years.
The X7 enables better solutions for Toivalan Metalli's customers, allowing for the rapid production of a wide array of high-quality parts at lower costs. Looking ahead, Toivalan Metalli plans to expand their applications, incorporating press brake tooling, welding fixtures, and more into their operations. This expert group of Finnish trailblazers remains committed to pushing the envelope and delivering exceptional solutions for their customers.