THE CUSTOMER
Founded in 1997, BODUK's predecessor was Japan's first website dedicated to the import, development, and sale of drones and other radio-controlled equipment to consumers. When President Houe Ohta anticipated a decline in drone popularity, he pivoted the company towards the industrial drone market, launching BODUK Co., Ltd. in 2002 to focus on enhancing infrastructure inspections with unique drone products. This strategic shift significantly reduced BODUK’s drone manufacturing time to between one-half and one-third of the original duration by using materials and labor more efficiently.
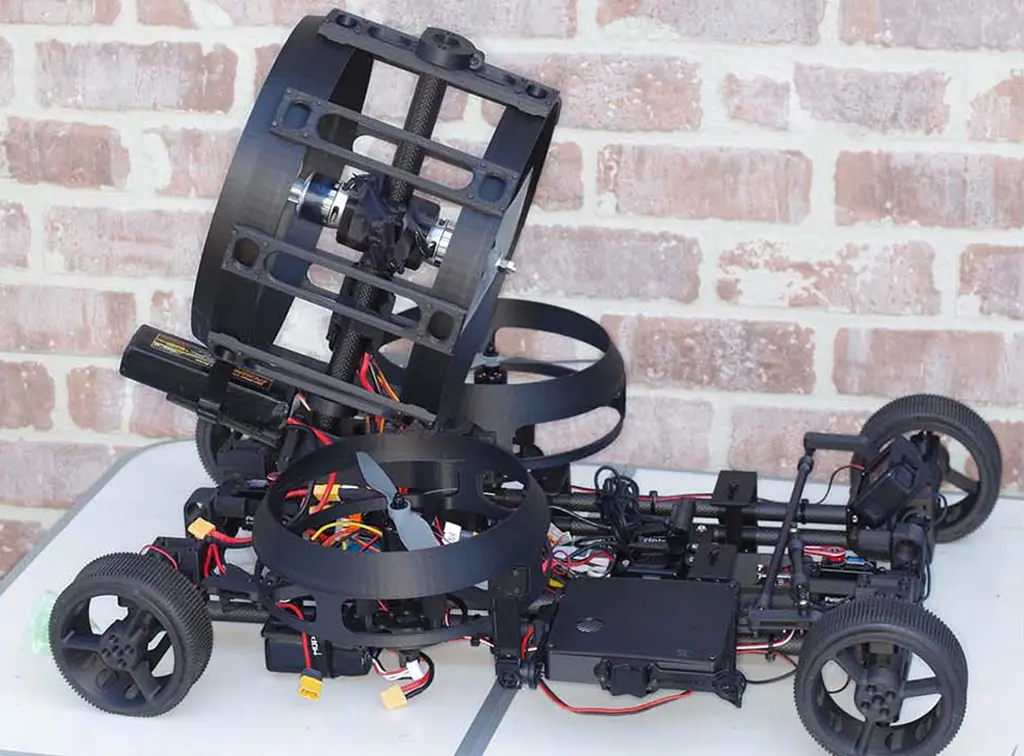
THE CHALLENGE
“Can they be used for inspecting large structures like buildings, bridges, and dams?” wondered Ohta, a civil engineering professional. At that time, drones were primarily used to collect and transmit video and temperature data. Ohta aimed to advance drone technology for non-destructive inspections, which collect internal data about a structure's integrity using methods like striking a concrete wall or applying electromagnetic waves.
A crucial component for this work is a proximity sensor, which, when mounted on a drone, needed a frame as lightweight as possible. “Depending on the type and size of the inspection equipment, the weight of the frame needed to support 1 kg of equipment is about 3 kg,” explained Ohta. The sensor frame also needed to withstand harsh environments.
For mass production via 3D printing, the printer needed to maintain reproducible precision for reliable assembly. Many 3D printers Ohta evaluated struggled with this level of precision.
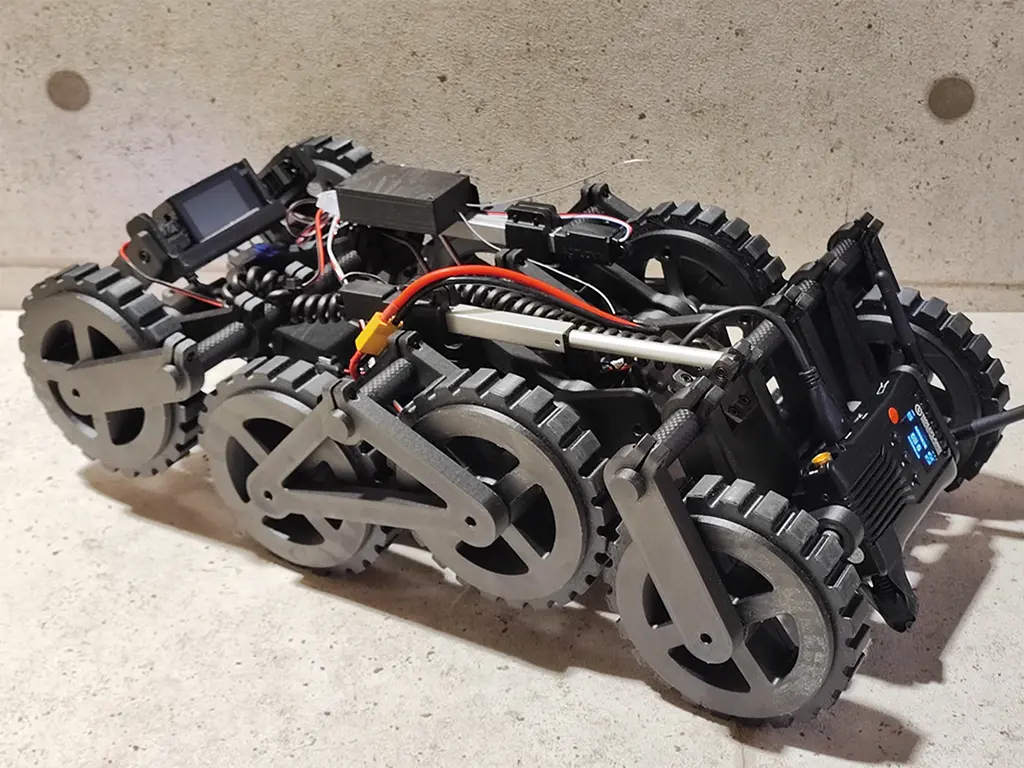
THE SOLUTION
In 2017, BODUK invested in Markforged Onyx One and Mark Two printers, and now operates 15 Markforged machines, including X7 industrial printers. Increasing the number of printers has significantly boosted BODUK’s manufacturing efficiency.
“With distributed batch processing, increasing the number of units is more effective than raising the speed of one unit, and it also helps us mitigate risks. For example, adding three units increases productivity by five times rather than three times,” explained Ohta.
Markforged products have met BODUK’s requirements for strength and flexibility, exemplified by their 3D-printed propeller guards made from carbon fiber. This material offers the perfect balance of toughness and flexibility, protecting the propeller without interfering with its function.
The reproducible precision of Markforged printers is evident in the smooth connections between BODUK’s drone parts, using 50 mm carbon rods to align and connect 13 parts. “The Markforged 3D printers can achieve this precision within 0.02 mm,” asserted Ohta.
Overall, Ohta is very satisfied with the performance and precision of his Markforged printers:
“Their good yields reduce labor costs and allow people to work without stress. We’re also satisfied with the high precision reproducibility achieved through the linear guide. In short, they’ve been very cost-effective.”
Ohta estimates that Markforged equipment reduces manufacturing time to between one-half and one-third compared to competing printers. “Reducing lost time not only cuts down on hidden costs, but it also frees up more time for improved product development,” he added.
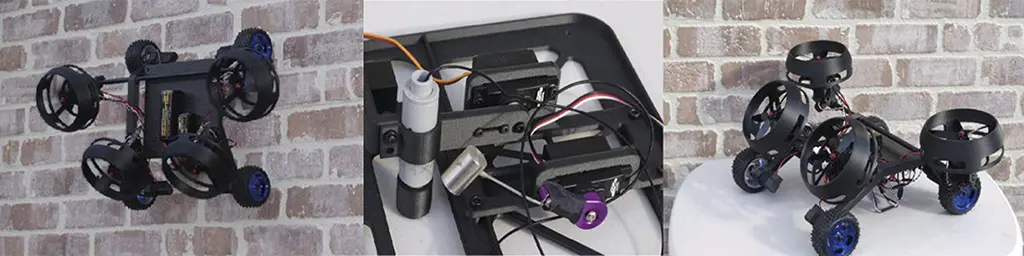
THE FUTURE
BODUK’s expertise in developing aerial vehicles fuels its innovation in industrial drones, including wall-climbing robots. The next phase involves developing and commercializing mobile robots for under-floor inspections, targeting applications in narrow spaces that are difficult for human inspectors to access.
“I believe there’s still potential to generate demand in the construction and civil engineering industries. For example, one possible application could be an inspection jig used at a highway maintenance site, primarily acting as a guide to aid manual labor by workers,” Ohta envisions.
With Markforged printers, there’s every reason to believe Ohta will transform many of his ideas into innovations benefiting the industries his company serves.
“What’s important is that good yields reduce labor costs and allow people to work without stress. We’re also satisfied with the high precision reproducibility achieved through the linear guide. In short, it’s been very cost-effective.”
– Houe Ohta, President, BODUK Co., Ltd.
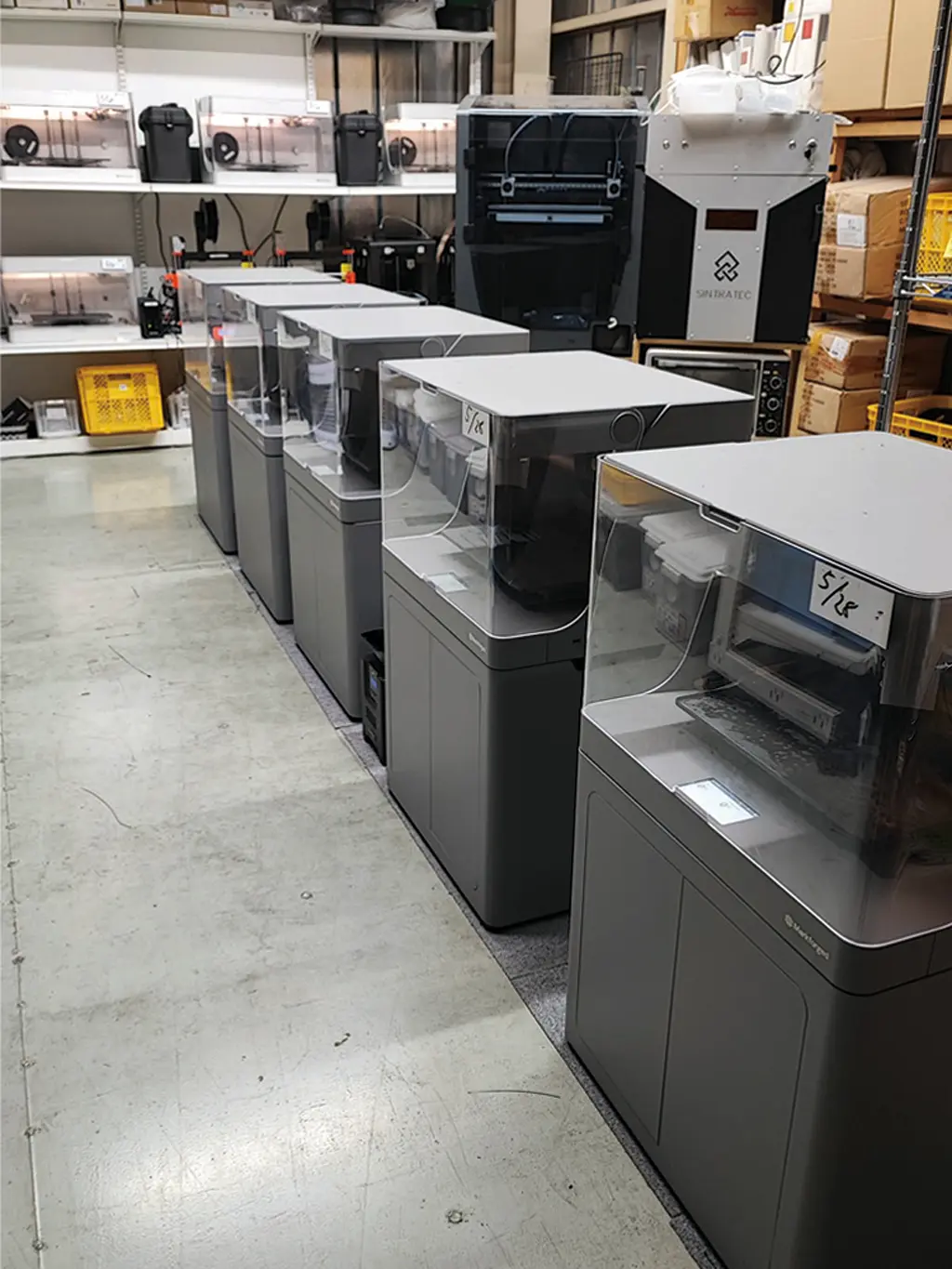