In the dynamic realm of additive manufacturing, the Markforged Metal X 3D printer has emerged as a game-changer, eliciting considerable attention and curiosity from the manufacturing community. With the tantalizing prospect of fabricating robust metal parts endowed with remarkable strength and precision, all from the convenience of a desktop printer, the Metal X holds the potential to reshape how industries approach production. As an industry expert with a wealth of experience in additive manufacturing, I had the privilege of immersing myself in the intricacies of the Metal X system. In this comprehensive review, I delve into the depths of its capabilities, scrutinize its performance across diverse applications, and contemplate the profound impact it might wield upon the manufacturing landscape.
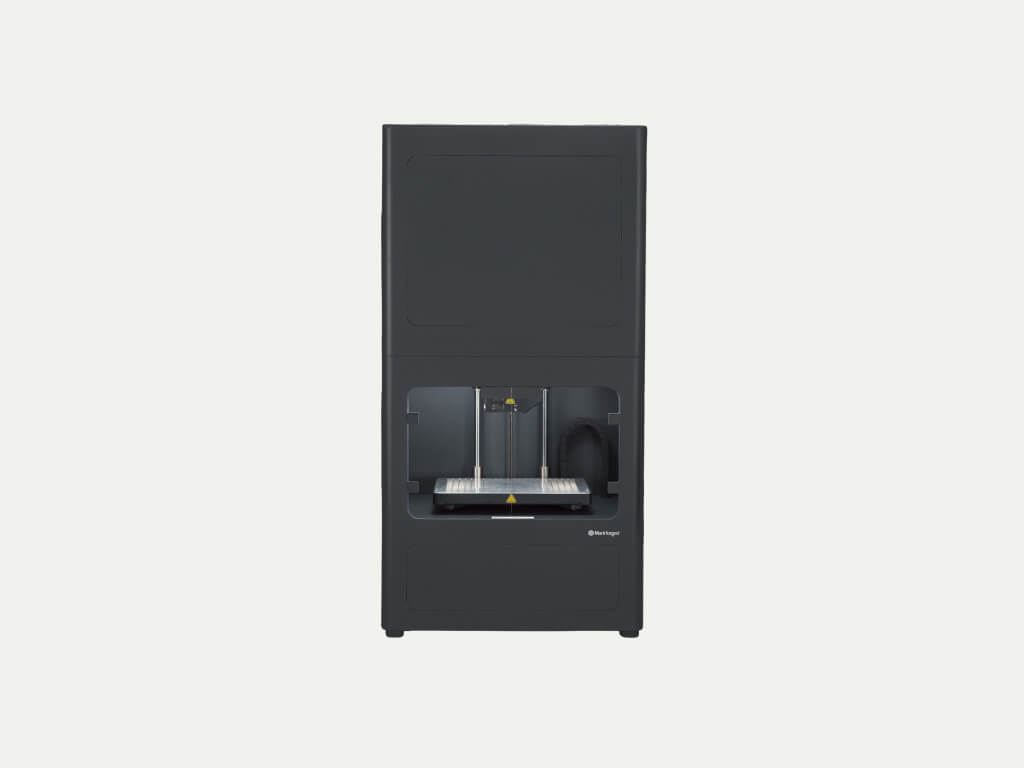
Build Quality and Design:
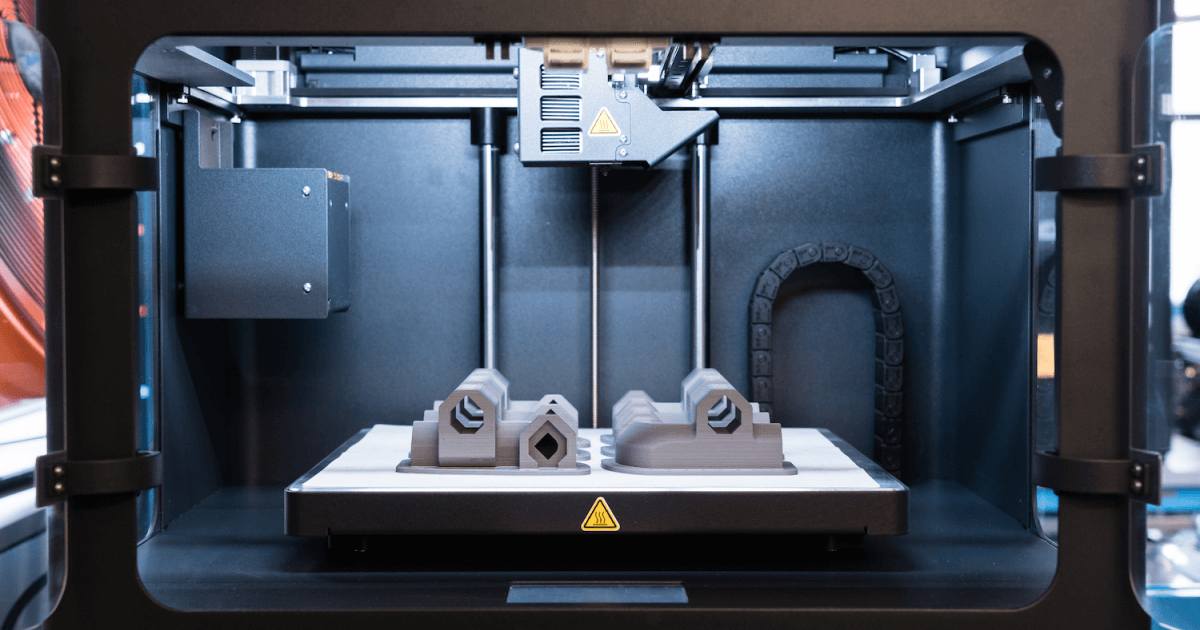
At first glance, the Markforged Metal X is a fusion of engineering precision and industrial aesthetics. The printer's build quality is robust, exuding reliability and durability that align seamlessly with its intended professional use. Its compact form factor is augmented by the judicious use of high-quality materials, creating a well-constructed machine that resonates with the demands of industrial environments. Moreover, the design emphasises user-friendliness, exemplified by the accessible build chamber and an intuitive touchscreen interface that eases operation and expedites the learning curve for new users.
Material Selection and Compatibility:
One of Metal X's standout features is its versatility in handling a variety of metals, including stainless steel, tool steels, Inconel, and more. This expansive range of materials is made possible through Markforged's proprietary metal printing process—Atomic Diffusion Additive Manufacturing (ADAM). This innovative approach blends metal powder with polymer binders to form a 'green part,' which is subsequently sintered to achieve full metal density. However, it's important to acknowledge that material choices are somewhat constrained, as they are limited to the pre-approved metal powders provided by Markforged. While this limitation may deter certain design ambitions, it serves to ensure optimal process parameters and print quality.
Print Accuracy and Surface Finish:
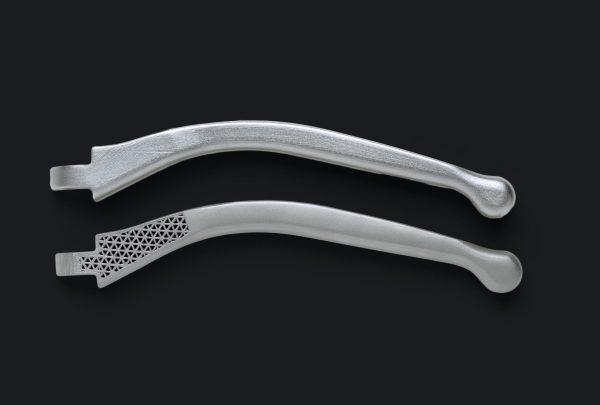
In the crucible of precision and accuracy, the Markforged Metal X demonstrates its mettle. With layer resolution and precision aligned with established industry benchmarks for metal 3D printing, the system is well-equipped to reproduce intricate geometries and elaborate designs. A noteworthy triumph lies in the post-sintered parts' impeccable surface finish—a testament to the printer's proficiency in reducing the need for laborious post-processing steps, a common hurdle in the additive manufacturing landscape.
Mechanical Properties:
The true hallmark of the Metal X lies in its ability to impart extraordinary mechanical properties to its printed parts. Exhibiting commendable tensile strength and fatigue resistance akin to traditionally manufactured components, the Metal X transcends its label as a mere prototyping tool. Its capacity to churn out end-use parts with unwavering mechanical integrity positions it as a formidable contender across industries. From aerospace and automotive to medical applications, the printer's creations stand as a testament to the potential of additive manufacturing to supplant conventional manufacturing methodologies.
Print Speed and Throughput:
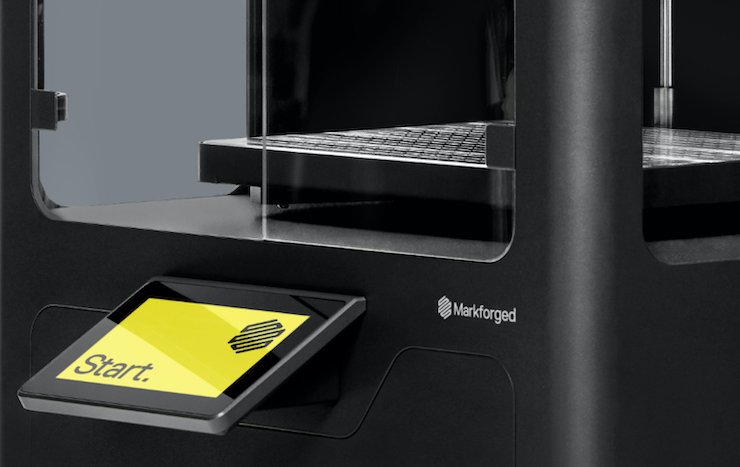
A recurring point of consideration in additive manufacturing is the interplay between speed and quality. Herein lies an area where the Metal X, while undeniably impressive, treads a delicate balance. The two-step ADAM process, encompassing the printing of the green part and subsequent sintering, engenders a time-consuming endeavour. While Markforged has made commendable strides in optimising print times, the dichotomy between the desire for rapid production and the need for mechanical excellence remains. The option to batch parts mitigates this concern, offering a trade-off between throughput and individual part complexity.
Cost Considerations:
Delving into the realm of industrial additive manufacturing necessitates grappling with multifaceted cost dynamics. The investment in a Markforged Metal X encompasses not only the initial capital outlay but also ongoing expenses encompassing metal powders, consumables, and maintenance. In the context of substantial production volumes, the cost per part becomes increasingly competitive when juxtaposed against traditional manufacturing paradigms. However, for smaller production runs or the creation of prototypes, the cost-effectiveness of the Metal X may be less pronounced.
In the crucible of innovation, the Markforged Metal X emerges as a pioneering force within additive manufacturing. Its capacity to metamorphose raw metal powders into robust, high-precision components underpins a new era of production possibilities. Yet, adopting the Metal X requires a nuanced assessment, considering application-specific requisites, batch sizes, and the intricate dance of costs. As the technology matures and embarks on an evolutionary trajectory, the Markforged Metal X stands poised to exert a transformative influence on manufacturing norms. With its impressive mechanical prowess, exceptional part quality, and the promise of redefining production paradigms, Metal X beckons industries to embrace its potential and spearhead the next phase of additive manufacturing innovation.
About the author:
“As a prominent 3D printer supplier in Ireland, our role extends beyond merely providing equipment. We understand the vital role we play in introducing cutting-edge technologies to our clients. The Markforged Metal X signifies a monumental leap that has the potential to reshape industries across the country. Our mission is to bridge the gap between innovation and implementation, offering businesses access to state-of-the-art 3D printing solutions that foster growth, efficiency, and competitiveness.” – James Wall
This comprehensive review of the Markforged Metal X is brought to you by James Wall, the founder of 3D Technology Ltd - an esteemed provider of cutting-edge 3D printing solutions in Republic of Ireland and Northern Ireland.